Ball Mills Initially
.jpg)
A Review of the Grinding Media in Ball Mills for Mineral
2023年10月27日 — The ball mill is a rotating cylindrical vessel with grinding media inside, which is responsible for breaking the ore particles Grinding media play an important role in the comminution of mineral ores in these mills2024年6月3日 — This article presents an overview of the fundamental principles underlying ball milling technology, encompassing aspects such as ball milling pretreatment, biochar Research progress on synthesis mechanism and performance 2024年1月26日 — Ball milling is a representative mechanochemical strategy that uses the mechanical agitationinduced effects, defects, or extreme conditions to activate A contactelectrocatalysis process for producing reactive First published on 9th January 2019 Abstract Ball milling is a simple, fast, costeffective green technology with enormous potential One of the most interesting applications of this technology in the field of cellulose is the Ball milling: a green technology for the
.jpg)
Ball Mill an overview ScienceDirect Topics
Ball mills give a controlled final grind and produce flotation feed of a uniform size Ball mills tumble iron or steel balls with the ore The balls are initially 5–10 cm diameter but 2017年5月1日 — A planetary ball mill was used to enable the grafting monomer to penetrate the nanoparticle agglomerates and initiate polymerisation reactions on the particles Fabrication of polymer nanocomposites via ball milling: Present Ball milling is a process, in which the moving balls apply their kinetic energy to the milled material, break chemical bonding and produce fresh surfaces by fracturing material particles The dangling bonds on the newly created Ball milling : a green mechanochemical approach 2021年11月17日 — Abstract This study investigates the effect of using ethanol as the process control agent during the wet ball milling of niobium (Nb) Dried nanocrystal Nb Wet ball milling of niobium by using ethanol, determination
.jpg)
High‐Energy Ball Milling as a General Tool for Nanomaterials Synthesis
2015年3月23日 — This chapter reports some fundamental thermodynamic and kinetic aspects of the highenergy ball milling (HEBM) technique HEBM technology consists in 2024年3月7日 — Initially, the raw materials are prepared in dry form, typically through crushing or grinding processes, to achieve the desired particle size and consistency The application of drygrinding ball mills in mineral processing provides significant advantages in terms of costeffectiveness, environmental sustainability, and process control Application of Dry Ball Milling in Mineral Processing2024年8月8日 — Unlock the secrets to ball mill efficiency with our comprehensive guide on choosing the right grinding media Learn how material composition, size, shape, hardness, and cost impact your milling Ball Mill Success: A StepbyStep Guide to 2023年10月27日 — The ball mill is a rotating cylindrical vessel with grinding media inside, which is responsible for breaking the ore particles Grinding media play an important role in the comminution of mineral ores in these mills This work reviews the application of balls in mineral processing as a function of the materials used to manufacture them and the A Review of the Grinding Media in Ball Mills for Mineral
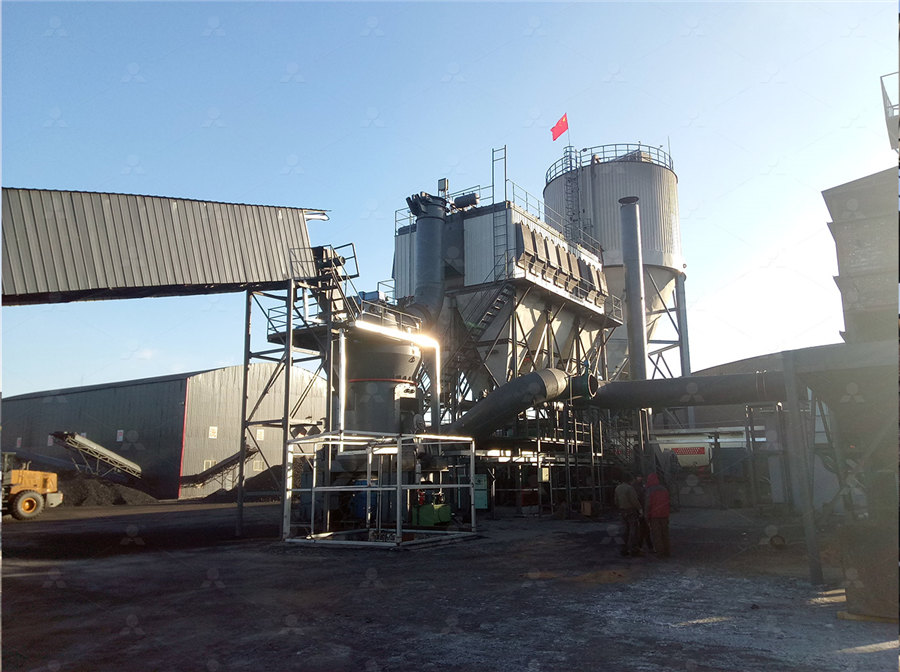
Pengertian Ball Mill dalam Proses Manufaktur PT Nihona
2023年10月27日 — Pada artikel ini, kita akan membahas pengertian ball mill dalam proses manufaktur Ball mill adalah peralatan yang sangat penting dalam berbagai industri, terutama dalam dunia manufaktur Kami akan membahas apa itu ball mill, bagaimana cara kerjanya, dan mengapa ball mill begitu penting dalam proses manufaktur Mari kita mulai! 2021年9月15日 — In this research, in order to find a suitable range for the number of lifters in the liner of ball mills, the DEM method is utilized Initially, a pilotscale ball mill with dimensions of 20 m × Determining an appropriate range for the number of cuboid 2024年9月15日 — The grinding efficiency is expressed in terms of percent loss, which represents how much material was ground up compared to what was initially fed into the ball mill What are the grinding efficiency of ball mills? The grinding efficiency of ball mills is directly correlated to the size and design of the ball millGrinding efficiency of ball mill calculating equationBall mill grinding machines are valuable tools in various industries, offering efficient and reliable grinding and mixing capabilities Understanding their working principle, different types, parts, applications, advantages, and recent developments helps to appreciate their significance and wideranging applications in industries such as cement Ball Mill Grinding Machines: Working Principle, Types, Parts
.jpg)
AXIAL TRANSPORT IN DRY BALL MILLS CFD
2003年11月26日 — The ball mill is initially uniformly filled with rocks and balls which are perfectly mixed Figure 3 shows the charge in the mill after 4 minutes of rotation (at 75% critical) The charge has been clipped by a vertical plane passing down through the center of the mill so that the2020年9月20日 — In respect of the particle strength and shape, a feed charge prepared using jaw and roll crushers is quite different from the one produced by grinding the material in the test ball mill Initially, for some time the crushed material is found to break in the ball mill at a significantly higher rate (20–30% is quite common) as compared to the Effect of particulate environment on the grinding kinetics of The balls form the grinding medium of the ball mill These balls are usually made up of steel, ceramic, flint pebbles, or hard rubber The inner wall of the shell is generally contains a coating of abrasion resistant material, eg, manganese steel or rubber Rubber lined (or coated) ball mills cause less wear to the productsBallmilling – Nanoscience and Nanotechnology I2024年9月9日 — The mill balls’ size is initially 30–80 cm in diameter but gradually wears away as the ore is ground In general, the ball mill grinder can be fed either wet or dry The ball mill machine is classed by electric Ball Mills Industry Grinder for Mineral
.jpg)
Investigating the effect of process variables for ball milling
2024年1月11日 — The ball mill is the most used in the literature Even though this technology has advantages, energy demand and scaleup are its most significant drawbacks 75% of the maximum value for the mill, since it is lower than the critical speed, for safety reasons and to operate the mill properly Initially, the required mass of beech chips and 2023年4月28日 — A planetary type ball mill is economical, simple to operate, and ideally suited for smallquantity batch type synthesis of powders and alloys and for reactive processing of powders The size of the jar and balls, rotational speed, milling duration, balltopowder ratio, jar material, milled material, and temperature are the most important Parametric study on four station ball mill for synthesis of 2019年10月18日 — General ball mill initially loaded ball, the size of the steel ball, the number, proportion, which aspect is added wrong, will directly affect the grinding efficiency of the ball mill In addition, in the process of grinding, the steel ball after high intensity grinding, resulting in wear, breakage, loss of round, will also reduce the grinding How to Fill the Ball Mill with Steel Balls for the First Time?2017年8月24日 — In Spex ball mill, the maximum temperature was 200 °C It was shown that the temperature of the balls was largely dependent upon milling speed and size of the balls In general, as shown in Figs 27 and 28, with increase in milling time, initially a rapid grain refinement was HighEnergy Ball Milling Parameters in Production of
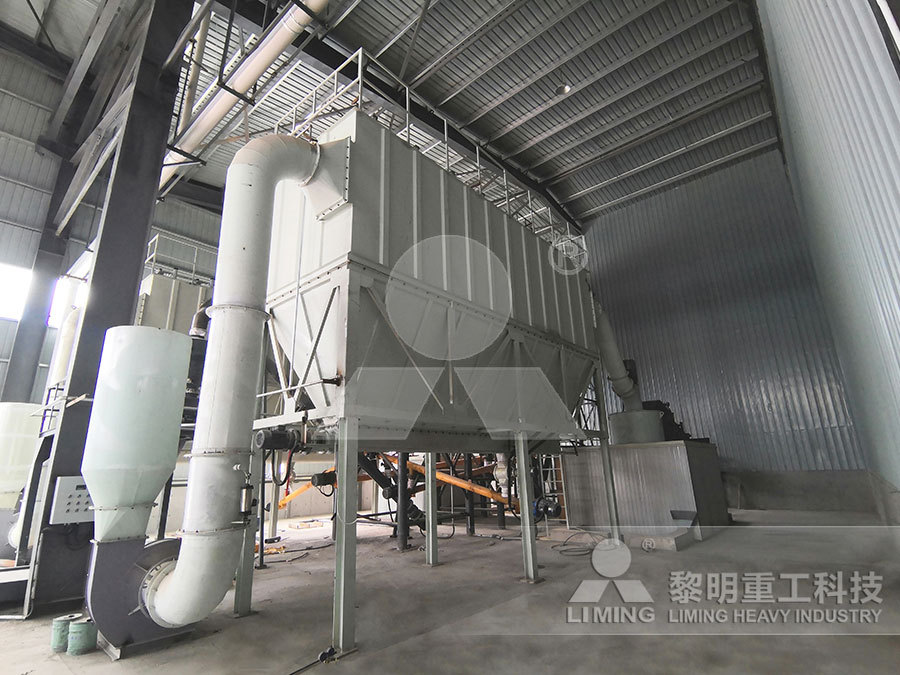
Recent Developments on the Synthesis of Nanocomposite
2022年9月16日 — In wet ball mills, a surfaceactive media is introduced to inhibit the formation of aggregates while dry mills are free of solvents and the attrition of particles occurs through powdertopowder friction Initially, the chemical ingredients are smashed between the balls during continuous collision Secondly, the sequence of materials 2024年6月12日 — A ball mill is a type of complex grinding device Having knowledge of its chargeload behavior is key to determining the operating conditions that provide the optimum mill throughput An elaborate description of the charge movement inside the ball mill is essential This study focuses on a laboratoryscale ball mill and utilizes a discrete Research on an Accurate Simulation Modeling and Charge 2014年1月1日 — Initially, detailed experimentation was carried out in a 254 cm diameter batch mill and a relationship for mill scaleup using a linear population balance model in wet grinding systems was (PDF) Population balance model approach to ball mill 2023年5月15日 — Ballmills are categorized into four types depending on the motion generated to produce momentum in grinding balls and act upon the material with various milling forces TV, SV, and FV, but the solubility and SP increase In the case of PT, the values initially decrease Still, as the milling energy increases with time, the PT values Ballmilling: A sustainable and green approach for
.jpg)
Insights into advanced ball mill modelling through discrete
2018年10月1日 — 1 Introduction Mathematical modeling of tumbling ball mills has evolved tremendously over the last 70 years or so From the empirical sizereduction relationships (Charles, 1957, Bond, 1952, Morrell, 2004) to the traditional population balance model (Austin et al, 1984, Herbst and Fuerstenau, 1980) and the more recent mechanistic 2018年7月1日 — Within the circuit, the feed is ground in the ball mill initially Mill filter sweeps the material (bluecoloured line) mainly from the second chamber of the ball mill and noncollected material overflows from the discharge Afterwards, the two streams (mill product and filter) are combined and sent to the high efficiency classifier via an Energy and cement quality optimization of a cement grinding circuit2021年3月12日 — Ball mills and grinding tools Cement ball mills are typically twochamber mills (Figure 2), where the first chamber has larger media with lifting liners installed, providing the coarse grinding stage, whereas, in the second chamber, medium and fine grinding is carried out with smaller media and classifying linersBALL MILLS Ball mill optimisation Holzinger Consulting2006年11月1日 — The ball mill is initially uniformly filled with rocks and balls which are perfectly mixed Fig 3 shows the charge in the mill after 4 min of rotation (at 75% critical) The charge has been clipped by a vertical plane passing down through the center of the mill so that the internal distribution of particles can be seenAxial transport in dry ball mills ScienceDirect
.jpg)
How to Fill the Ball Mill with Steel Balls for the First Time?
2019年10月18日 — General ball mill initially loaded ball, the size of the steel ball, the number, proportion, which aspect is added wrong, will directly affect the grinding efficiency of the ball mill In addition, in the process of grinding, the steel ball after high intensity grinding, resulting in wear, breakage, loss of round, will also reduce the grinding 2016年1月1日 — The wear of balls used during a grinding process is considered one of the losses that cause an increase in the operating cost allocated to the ball mill [21] Ball wear occurs due to abrasion (PDF) A comparison of wear rates of ball mill grinding media2001年8月1日 — Initially, a semiindustrial ball mill with dimensions of 20 m × 111 m without any lifter is simulated Afterwards, by insetting 1,2, 4, 8,16,20,26,30, and 32 cuboid lifters with dimensions of Charge behaviour and power consumption in ball mills: The team at Surplus Record has developed this useful Mill Buying Guide, which focuses on some of the most popular mills available: The Ball Mill, Pebble Mill and SAG Mill Included you will find an array of topics including: the basics of how mills work, some tips and tricks to keep in mind, and what to look for when searching for the best used Ball, Pebble and SAG Mills: A Buyers Guide Surplus Record
.jpg)
Ball Mills in the Mineral Processing Industry MechProTech
2024年5月27日 — Ball mills are widely used in the beneficiation process for various ores and minerals, including gold, copper, iron, and zinc They fall part of the comminution process, where ores are crushed to separate valuable minerals from the gangue In mineral processing plants, ball mills are employed in grinding circuits to reduce the particle size of Ball mills give a controlled final grind and produce flotation feed of a uniform size Ball mills tumble iron or steel balls with the ore The balls are initially 5–10 cm diameter but gradually wear away as grinding of the ore proceeds The feed to ball mills (dry basis) is typically 75 vol% ore and 25% steelBall Mill an overview ScienceDirect TopicsBall milling technique, using mechanical alloying and mechanical milling approaches were proposed to the word wide in the 8th decade of the last century for preparing a wide spectrum of powder materials and their alloys In fact, ball milling process is not new and dates back to more than 150 years It has been used in size comminutions of ore, Ball Milling an overview ScienceDirect Topicsthe number of ball mill spins (initially 100 rotations) This to find the mass of fines produced by spin or revolution ( ), which represent a circulating load of 250% This is on the premise that more ball mill spins will produce finer particles, and therefore less circulating load (circulating load=coarseBond´s work index estimation using nonstandard ball mills
.jpg)
Morphology and wear of high chromium and austempered ductile iron balls
2021年11月1日 — All the specimens were initially austenitized at 927 °C (1700 °F) for 2 h The first batch of samples were processed by conventional singlestep austempering process at several temperatures such 2013年2月1日 — For the second issue, mixture breakage was initially conducted in the ball mill [18], and samples were pure minerals for the easy separation of progenies by floatsink test or chemical reaction Grindability of binary ore blends in ball mills Request PDFVertical roller mills have several advantages over traditional ball mills They have a lower energy consumption rate, have a smaller footprint, and can be operated at higher capacity and separation The material is initially fed into the mill through the inlet chute and then transported to the grinding table Once the material is on the How does a Vertical Roller Mill Work? ball mills supplier2020年12月1日 — The overflow ball mill used here is a 6 m diameter × 10 m long (external shell dimensions) design as was the case in the last section The belly liner and end wall lifter designs are the same as earlier and as used in [82] Key geometry changes needed to support use of this ball mill for secondary slurry flow grinding are: 1Advanced comminution modelling: Part 2 Mills
.jpg)
Combined DEM and SPH simulation of overflow ball mill
2017年7月1日 — For the DEM setup of the ball charge, the mill chamber is initially filled with a 34% volumetric fill of ball sizes ranging from 32 to 65 mm The full ball size distribution is given in Table 3 The number of particles in the DEM part of the model is around 135,0002024年1月26日 — a Schematic illustration of a ball mill process using triboelectric materials b Comparison between piezoelectric and contactelectrification (CE) effects, which suggests that catalyzing reactions A contactelectrocatalysis process for producing reactive Economy Ball Mill, a division of JSB Industrial Solutions, Inc manufactures Ball Mills that are diverse in applications and uses Since we are an OEM and our product line has been around for over 50 years, we can provide the experience and knowledge to enhance your process capabilities by applying our procedural based manufacturing methods to your Ball Mills Economy Ball Mill/JSB Industrial Solutions Inc2024年3月7日 — Initially, the raw materials are prepared in dry form, typically through crushing or grinding processes, to achieve the desired particle size and consistency The application of drygrinding ball mills in mineral processing provides significant advantages in terms of costeffectiveness, environmental sustainability, and process control Application of Dry Ball Milling in Mineral Processing
.jpg)
Ball Mill Success: A StepbyStep Guide to
2024年8月8日 — Unlock the secrets to ball mill efficiency with our comprehensive guide on choosing the right grinding media Learn how material composition, size, shape, hardness, and cost impact your milling 2023年10月27日 — The ball mill is a rotating cylindrical vessel with grinding media inside, which is responsible for breaking the ore particles Grinding media play an important role in the comminution of mineral ores in these mills This work reviews the application of balls in mineral processing as a function of the materials used to manufacture them and the A Review of the Grinding Media in Ball Mills for Mineral 2023年10月27日 — Pada artikel ini, kita akan membahas pengertian ball mill dalam proses manufaktur Ball mill adalah peralatan yang sangat penting dalam berbagai industri, terutama dalam dunia manufaktur Kami akan membahas apa itu ball mill, bagaimana cara kerjanya, dan mengapa ball mill begitu penting dalam proses manufaktur Mari kita mulai! Pengertian Ball Mill dalam Proses Manufaktur PT Nihona 2021年9月15日 — In this research, in order to find a suitable range for the number of lifters in the liner of ball mills, the DEM method is utilized Initially, a pilotscale ball mill with dimensions of 20 m × Determining an appropriate range for the number of cuboid
.jpg)
Grinding efficiency of ball mill calculating equation
2024年9月15日 — The grinding efficiency is expressed in terms of percent loss, which represents how much material was ground up compared to what was initially fed into the ball mill What are the grinding efficiency of ball mills? The grinding efficiency of ball mills is directly correlated to the size and design of the ball millBall mill grinding machines are valuable tools in various industries, offering efficient and reliable grinding and mixing capabilities Understanding their working principle, different types, parts, applications, advantages, and recent developments helps to appreciate their significance and wideranging applications in industries such as cement Ball Mill Grinding Machines: Working Principle, Types, Parts 2003年11月26日 — The ball mill is initially uniformly filled with rocks and balls which are perfectly mixed Figure 3 shows the charge in the mill after 4 minutes of rotation (at 75% critical) The charge has been clipped by a vertical plane passing down through the center of the mill so that theAXIAL TRANSPORT IN DRY BALL MILLS CFD2020年9月20日 — In respect of the particle strength and shape, a feed charge prepared using jaw and roll crushers is quite different from the one produced by grinding the material in the test ball mill Initially, for some time the crushed material is found to break in the ball mill at a significantly higher rate (20–30% is quite common) as compared to the Effect of particulate environment on the grinding kinetics of
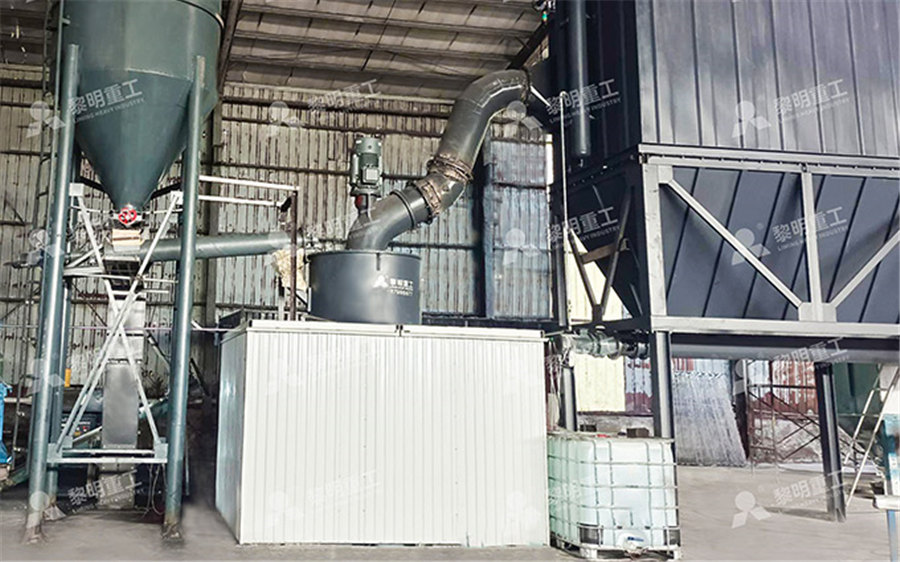
Ballmilling – Nanoscience and Nanotechnology I
The balls form the grinding medium of the ball mill These balls are usually made up of steel, ceramic, flint pebbles, or hard rubber The inner wall of the shell is generally contains a coating of abrasion resistant material, eg, manganese steel or rubber Rubber lined (or coated) ball mills cause less wear to the products